Performance Against Goal
Performance Summary 2023
Recordable Work-related Injuries Rate of Employee
Recordable Work-related Injuries Rate of Contractor
Lost Time Injury Frequency Rate (LTIFR) of Employee
Lost Time Injury Frequency Rate (LTIFR) of Contractor
High-consequence Work-related Injuries Rate(Excluding Fatalities) of Employee
High-consequence Work-related Injuries Rate (Excluding Fatalities) of Contractor
The number of fatalities as a result of work-related injury of Employee
The number of fatalities as a result of work-related injury of Contractor
Management Approach
Structure of the Occupational Safety, Health and Environment Committee
The Company strictly adheres to the law by appointing 1) an area-level Committee of Occupational Safety, Health and Working Environment that focuses on employee participation by electing representatives from employers and employees on a proportionate basis as required by law, and hosting monthly meetings. Beyond stipulation by the law, the Company has implemented Occupational Safety, Health and Environmental Management across all operational areas of the Company. Secondly, the Company has appointed 2) a function-level Sub Committee of Occupational Safety, Health and Working Environment that is elected every 2 years and has the responsibility of assessing issues from the area-level Committee of Occupational Safety, Health and Working Environment and budget approvals. Thirdly, the function-level Sub Committee of Occupational Safety, Health and Working Environment is under the supervision of 3) the Occupational Safety, Health and Environment Committee that is responsible for relaying the policy to each operation function and aligning the same standard with employees at every level within the organization, including contractors and suppliers across the Company’s supply chain.
Furthermore, the Company uses the evaluation of the risks toward Safety, Occupational Health and Working Environment to improve operation processes, work areas, and employee training as well as equipment in 7-Eleven stores.
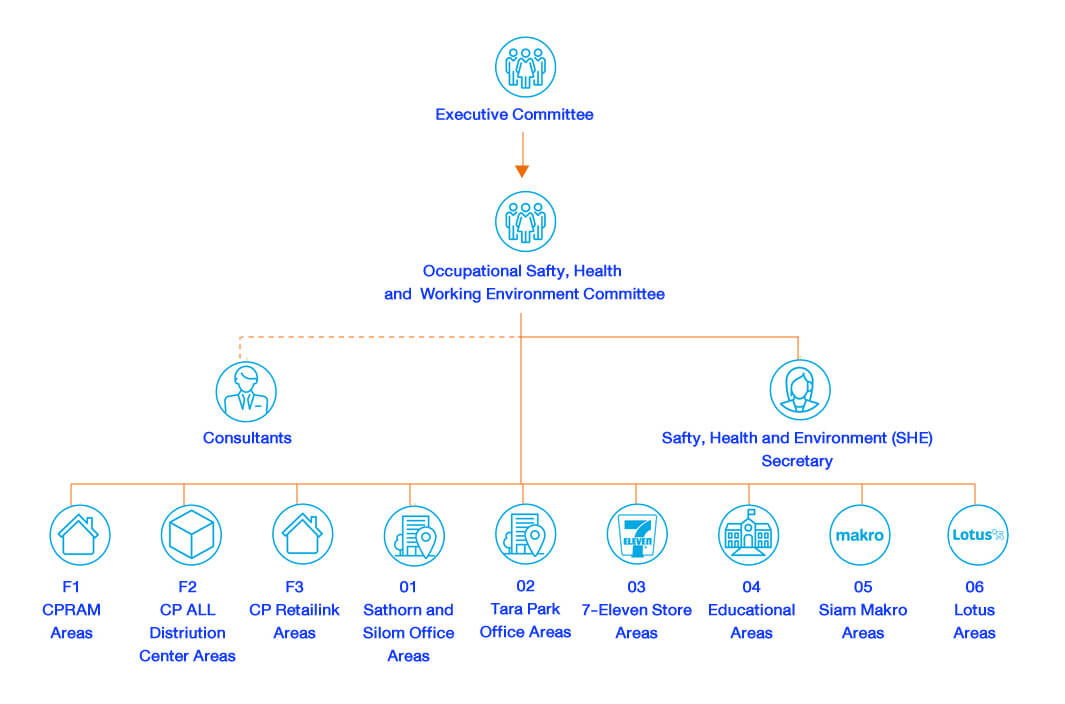
Elevate the Level of Occupational Health, Create a Safe Workplace
The Company prioritizes respecting occupational health, safety, and environmental aspects in the workplace, and safety during employees’ work time, including contractors who come to work in the company’s area. by establishing policies on safety, occupational health, and the environment in workplace, including managing and ensuring safe working conditions according to international standards to the law and aims to become an accident-free organization by 2030. Additionally, the Company has set up a committee for safety, occupational health, and workplace environment policies within the marketing and distribution business group. The Company set policies, operational guidelines, and plans to develop occupational health and safety systems, a committee has been established to evaluate the effectiveness of safety, occupational health, and environmental management, in collaboration with the Charoen Pokphand Group, to establish a committee for preventing severe accidents and minimizing potential impacts. Other activities include organizing a workshop seminar for the Occupational Safety, Health, and Environment Committee annually, as well as raising the level of management to the international level. The objective is to create a positive impact on the environment both inside and outside the organization. The Company ensures that employees work in safe working conditions.
OHS risk and hazard assessments to identify what could cause harm in the workplace
Risk Assessment Process
The Occupational Safety, Health and Environment Committee assigned executives at a department level or equivalent in each area to assess the risks to identify activities/area/work characteristics, such as driving a motor vehicle/motorcycle, chemicals, light, sound, by considering the work involved. Work from offsite areas that are at risk, including work related to contractors and including a review of risks in case of changes in control of raw materials / activities / processes / new products / flowcharts of workflow. There is also the case of new laws / complaints / accidents and risk reduction considerations once a year by assessing risks in both routine and normal situations; and irregular working situations that occur from time to time, along with assessing the risk of behavior affecting work activities, as well as identifying hazards and assessing the significance of the nature of safety problems under the 7 categories, consisting of 1) Environment 2) Machinery, tools, equipment 3) Materials / raw materials 4) Actions or behaviors (human behavior) 5) working conditions 6) Employees 7) Social Factors.
Then the organization jointly assesses the risks by using the criteria of 1) assessing the likelihood of loss from hazard 2) assessing the severity of the loss from hazard, and registering a risk to further prioritize and determine risk control measures.
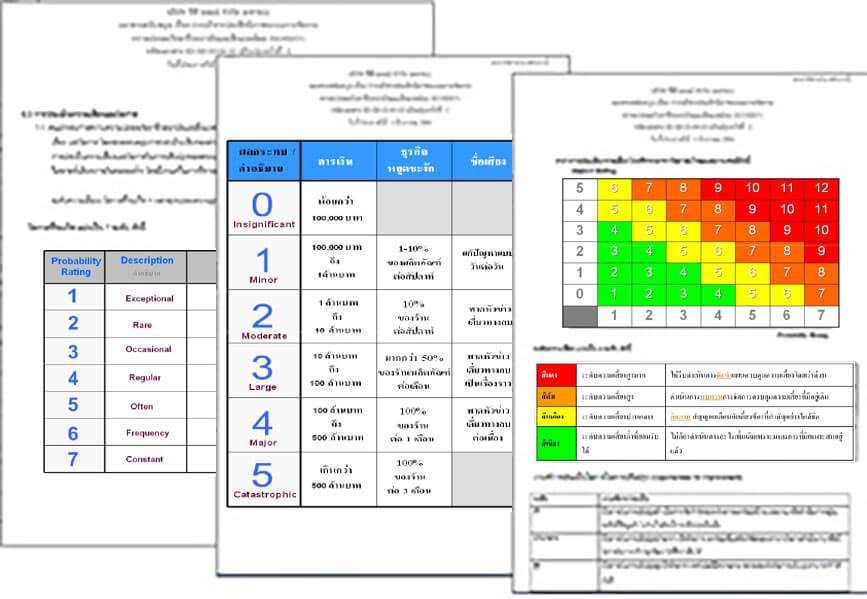
Prioritization and integration of action plans with quantified targets to address those risks
Those who are responsible for each area must prioritize risks to determine risk management measures and propose for approval from the Occupational Safety, Health and Environment Committee.
Risk Level | Detailed Operations |
---|---|
Unacceptable (5) | Stop the operation immediately and find solution to decrease the risk level to an acceptable level. There must an investigation into the causes and apply the solution before a permission to resume the operation is granted. There must also be controlling measures, and there must be evidence ready for investigation throughout an allotted time |
High (4) | Decrease the risk level to an acceptable level by revising the existing controlling measure / canceling / set a new measure / set objectives, goals, and projects, as well as there must be evidence ready for investigation throughout an allotted time |
Medium and Acceptable (2,3) | Reviewing the appropriateness of existing controlling measure to continuously control risk to stay at an acceptable level and a line manager must review the operation thoroughly |
Small (1) | A line manager must review the operation constantly |
In addition, they must assign it to relevant people to prepare a project action plan and to set project objectives, quantitative goals and responsible persons, and propose the Safety, Occupational Health and Work Environment Committee for consideration and approval of projects and plans. Read more about the project at —> Sustainability Report 2023 (Page. 157-165)
Project example, objectives, and goals
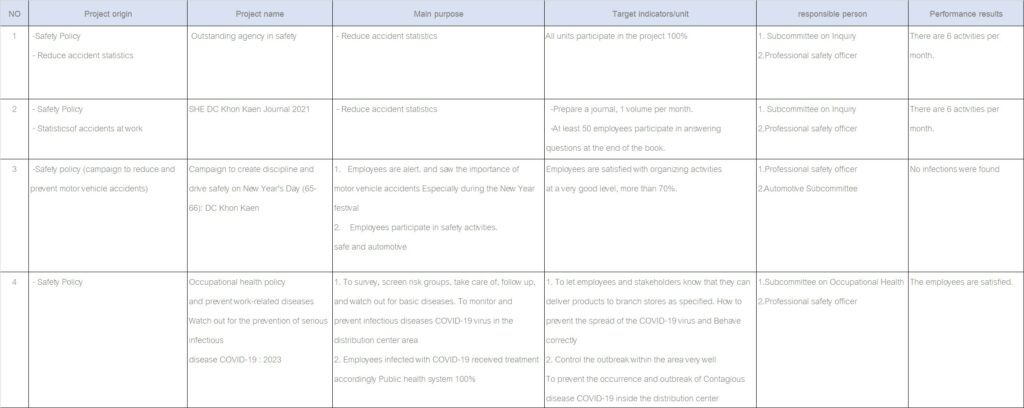
Project example, objectives, and goals
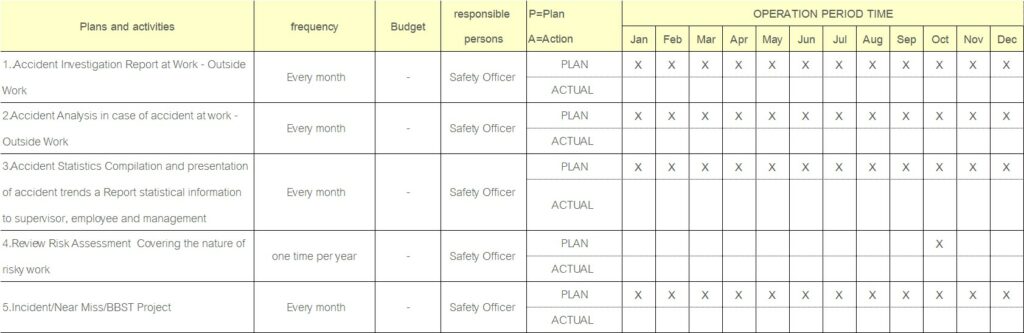
In addition, the Company provides opportunities for employees to report accidents and high-risk activities that occur through various channels. The Company also establishes procedures for investigating accidents. The Accident Investigation Committee is responsible for investigating, analyzing the accident, and determining appropriate solutions. From the safety risk assessment of employees and contractors, 5 high-risk activities were found, consisting of rider delivery, works by freight contractors, works by the repair contractor, forklift driving, and machinery-related works. In 2023, there were fatal accidents from 2 high-risk activities. Including the work of freight contractor works and rider delivery. The results of the investigation can be summarized as follows:
High-risk activities | Unsafe Situation (cause) | Unsafe Actions (cause) | Solution/Preventive Measures |
---|---|---|---|
Freight contractor works |
|
|
|
Rider Delivery |
|
|
Comply with the guideline from 7 Do’s 11 Don’ts
|
Occupational health and safety system development plan 2023
The Company develops occupational health and safety management in employees’ work areas, extending to contractors under the company’s supervision regularly. Additionally, guidelines are established to consider selecting areas ready for certification application, inspections by third-party auditors, and readiness before actual inspections, including conducting annual surveillance audits to maintain system standards. In 2023, the company obtained standard certification ISO45001:2018 covering a total of 21 areas, with 16 areas for re-certification and received additional certification in 5 areas, namely Chonburi Regional Distribution Center (RDC), Chonburi Temperature Controlled Distribution Center (CDC),Nakhon Sawan Regional Distribution Center (RDC),Nakhon Sawan Temperature Controlled Distribution Center (CDC),Nakhon Ratchasima Temperature Controlled Distribution Center (CDC). As a result, the Company’s target areas, of the company has been certified to cover 80% and there is a plan to expand in 2024, totaling 2 areas, namely Phuket Temperature Controlled Distribution Center (CDC) and ALL Complex Distribution Center
Occupational Health and Safety Management Standard Upgrade Plan Occupational Health and Safety (OHS) to the international standard ISO 45001: 2018
2019 (Phase1)
2020-2021
2022 (Phase 2)
2022 (Phase 2)
2023
Assess and monitor by Independent external verification of health, safety and well-being
SCA Evaluation Plan for Product Distribution Department in 2023
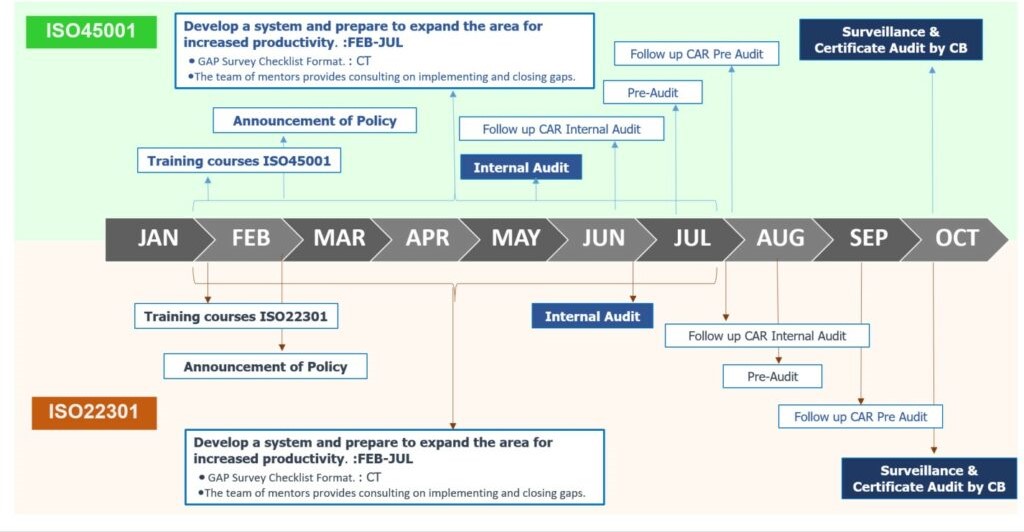
2023 : Re-Certificate 16 site
Dry Grocery Distribution Center
Chill Distribution Center
Frozen Distribution Center
Head Office
2023 : Certificate in 5 site
Dry Grocery Distribution Center
Chill Distribution Center
CPALL ISO 45001 Certificate for Nakhon Ratchasima (CDC&BDC ) CPALL ISO 45001 Certificate for Bangbuathong (DC ) CPALL ISO 45001 Certificate for Khonkaen (RDC )
Policy, Goal, and Safety and Risk Assessment
The Company establishes policies for safety, occupational health, and environmental conditions in the workplace, along with setting targets towards conducting business with reduced numbers and rates of work-related fatalities and injuries of employees and all subcontractors. The Lost Time Injury Rate (LTIFR) is aimed to decrease by 40% and reach zero by the year 2030. The Company has conducted a risk assessment in 4 main steps by identifying areas that may cause hazards in the workplace, namely 1) Identify activities, areas, and nature of work, 2) Identify hazards, 3) Assess risks and 4) Prepare a risk registry. This includes prioritizing and integrating action plans with quantitative goals to determine risk management measures. The information was ready to be submitted to the Committee on Safety, Occupational Health, and Environment to consider and approve the project and implementation of monthly and annual plans. The Company also facilitates a channel of communication for employees to report accidents that occurred or have high risks of occurring. The objective is to reduce, control, and prevent any accidents that may occur.
Integration of actions to prepare for and respond to emergency situations
The Company has integrated operations to prepare and respond to emergency situations.
An Example of the Operation
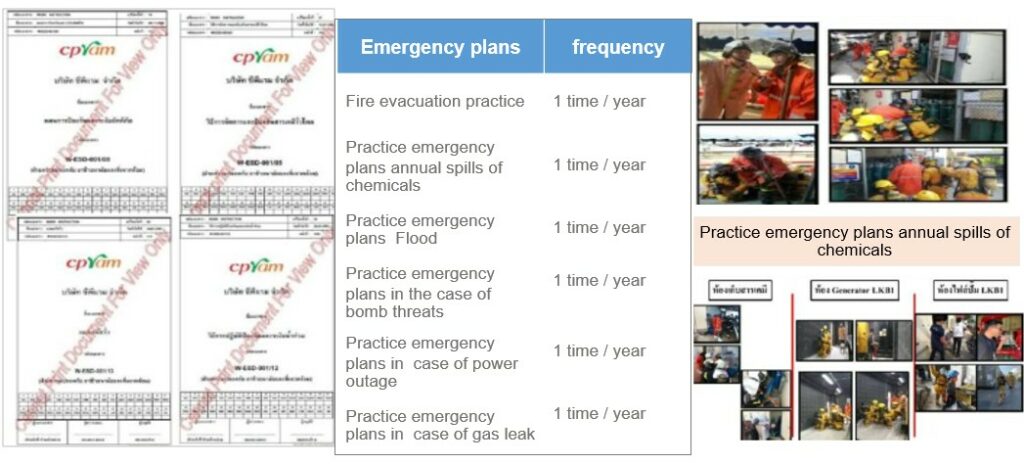
An Example of an Annual Emergency Plan Practice Schedule
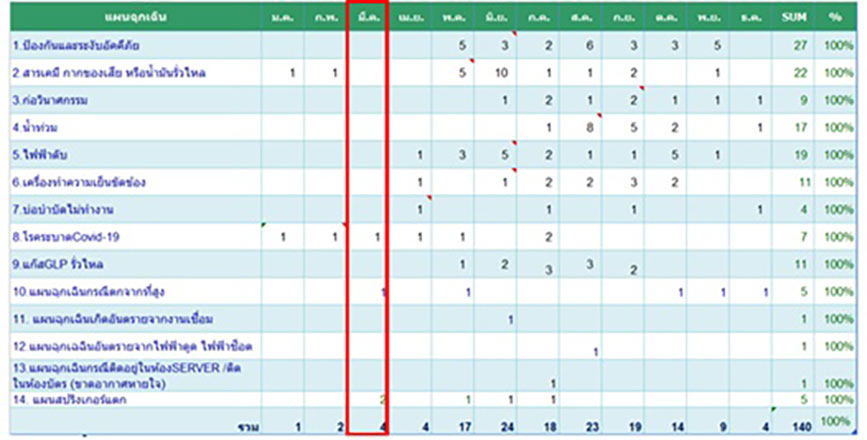
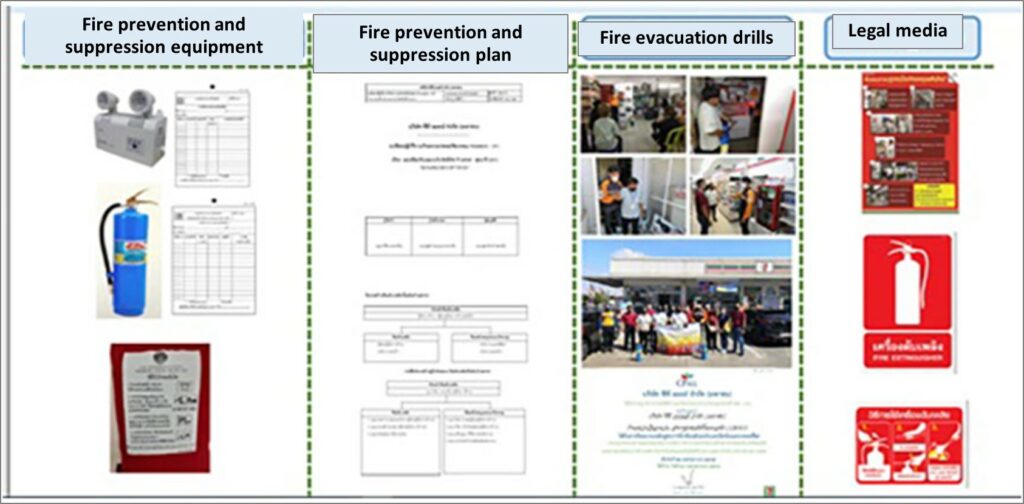
Evaluation of progress in reducing/preventing health issues/risks against targets
Occupational Safety, Health and Environment Committee evaluates and monitors the progress of projects and plans every month, both qualitatively, quantitatively, and proactively. Examples are checking the working environment, safety inspection according to the inspection plan of machinery, equipment, maintenance of machinery, equipment, health checks, and along with the objective review and goals of the project once a year.
Examples of Quantitative Tracking to Measure Progress of Objectives and Goals for 2023
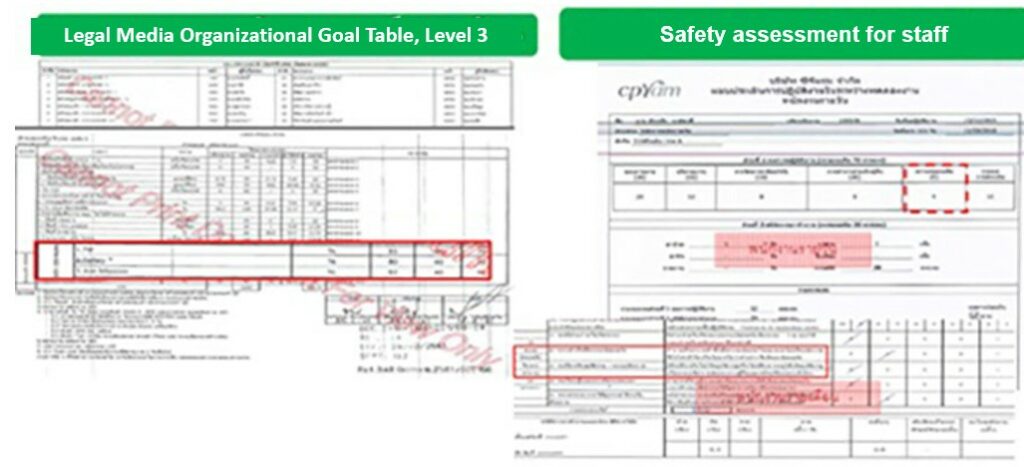
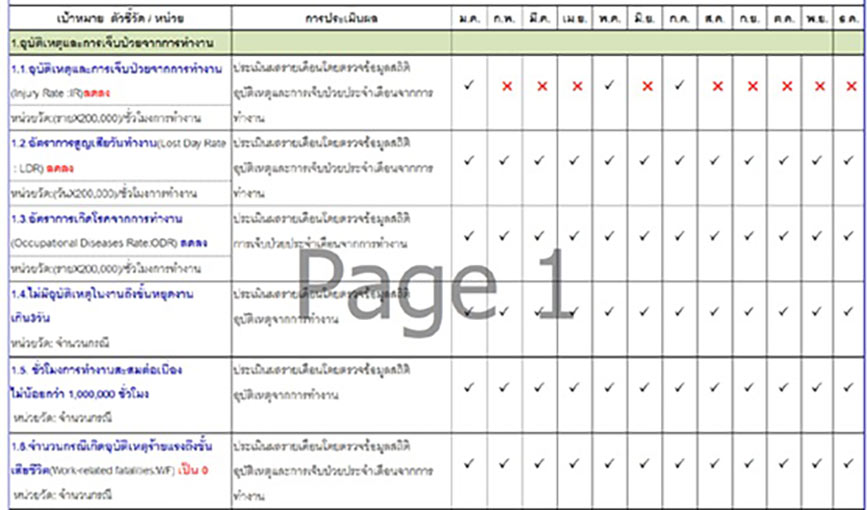
An example of the proactive monitoring of the safety of the 7-Eleven store’s operating line by the Quality Store Standard Inspector once a month
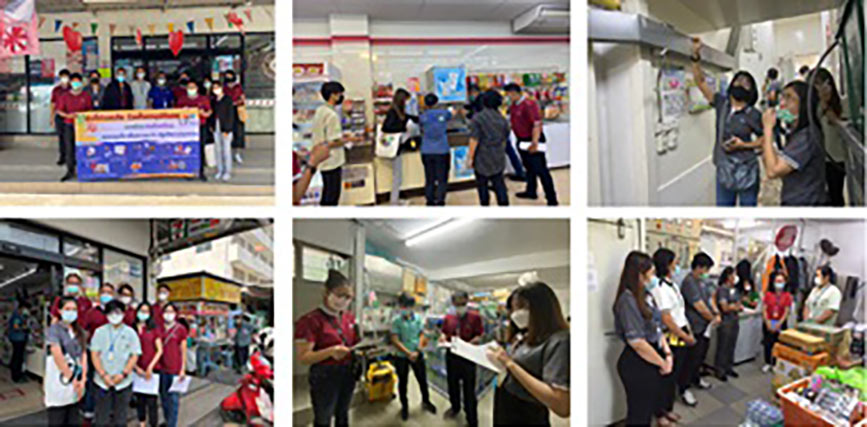
An example of proactive health checks based on risk factors
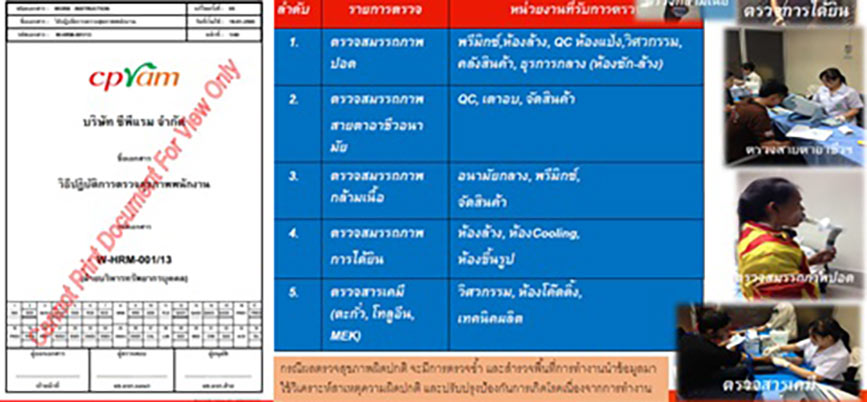
Internal inspections
The Company has established a systematic internal audit process to ensure that the occupational health management system and organizational safety has been implemented continuously and effectively. This is accomplished by collaborating with Charoen Pokphand Group to establish a Safety, Health and Environmental management effectiveness assessment program (SHE) to prevent serious accidents and reduce their impact. This is carried out by the central committee once a year under the criteria for evaluating the effectiveness of SHE as follows.
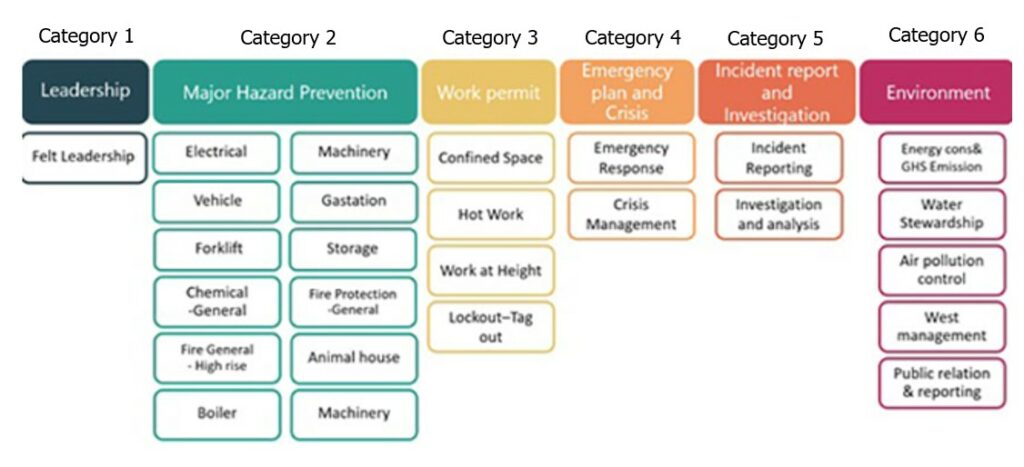
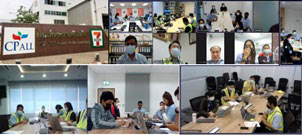

The Company has an integrated workflow to prepare for and respond to emergency situations, as well as operated with works related to safety, occupational health, and environmental conditions in the workplace, while also promoting a good quality of life for employees within the organization through three main programs, as follows:
1. Decent Quality of Life for Employees and Family Programองพนักงานและครอบครัวพนักงาน
Flexible Work Arrangement
The Company promotes work-life balance by allowing employees with permanent employment status to choose the following work schedules that are aligned with their lifestyle. The specified periods are as follows:
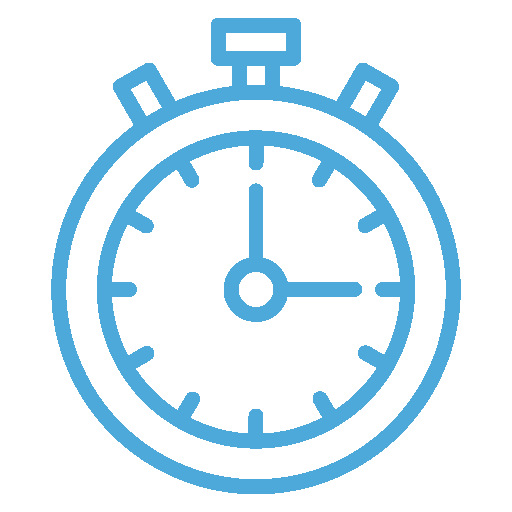
Time period
07.30-17.00
08.00-17.30
08.30-18.00
09.00-18.30
09.30-19.00
The Company also has a policy and guidelines allowing employers to choose their work location (“Work Anywhere”), in addition to being able to work from home for a maximum of 3 days each week as well as supporting a work system that supports work Option to work at any location So that employees can communicate and access systems to work efficiently, such as online meeting systems. Communication system via CP ALL Connect and True Virtual Connect, etc.
Welfare Program for Employees’ Families
The Company has started a trial program regarding healthcare benefits for inpatient cases (IPD) for employees’ parents, providing an option for employees who are single or those not using healthcare benefits for spouses to utilize healthcare benefits for their families. This aims to assist in sharing the financial burden of medical expenses and to motivate employees.
Furthermore, the Company prioritizes creating a good quality of life and fostering good relationships among both employees and their families. This aims to reduce employee stress and build strong ties to the organization. The Company supports benefits for the good quality of life of employees’ families, as follows:
![]() Organization of activities for children and relatives of employees and executives |
To lower parental burden, create a learning experience, and enable the productive use of their time. These include:
|
![]() Competency and Personality Analysis services for children and youth in the ” Luk Riang Children’s Fund” program |
|
Breastfeeding support in the workplace program
The Company has provided the following welfare for female employees who are preparing for motherhood, from pregnancy, and childbirth, to child-rearing. Through various projects such as organizing training to provide knowledge about breast milk for pregnant mothers. Activities to visit mothers after giving birth Providing a place for mothers to breastfeed. Within the operating area of CP All Distribution Center.
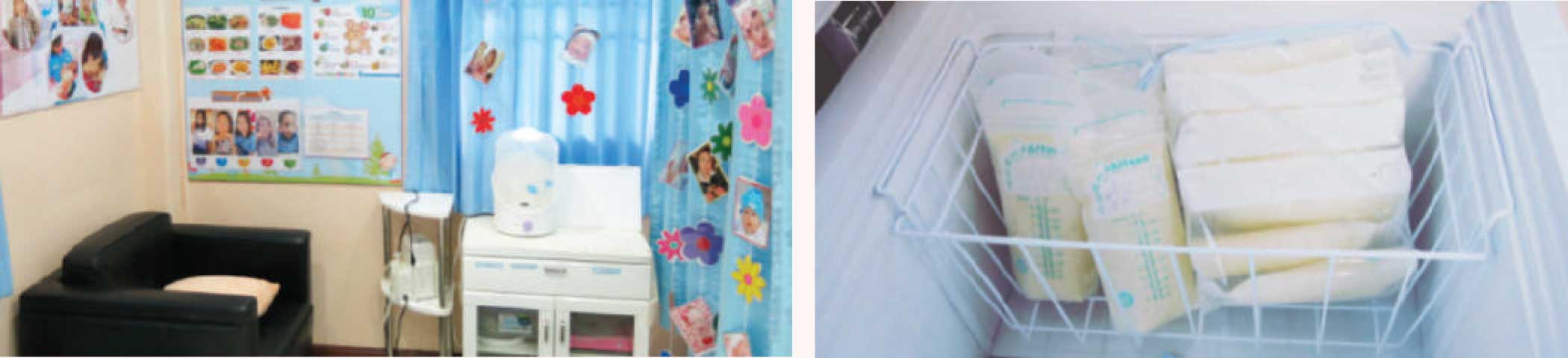
Impacts and Benefits
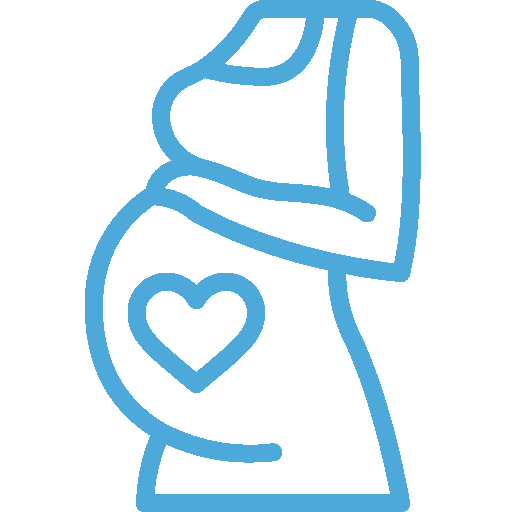
Reduced turnover employees following childbirth
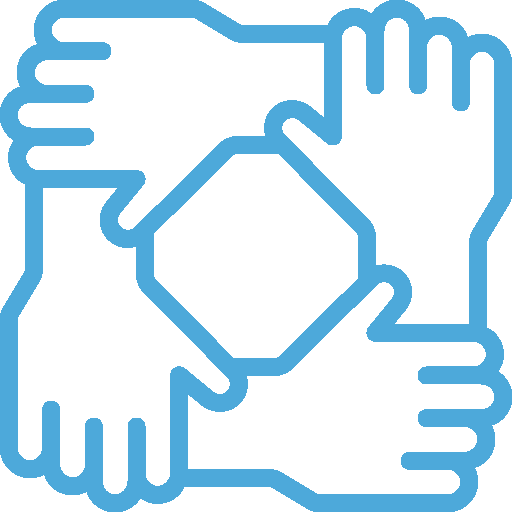
Fosters good employer-employee relationship
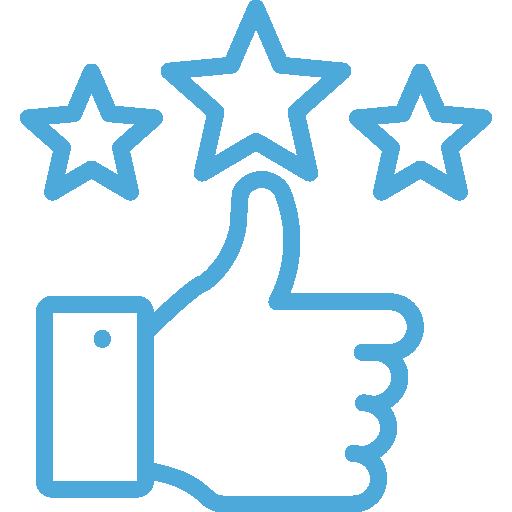
employee satisfaction
Health for ALL
The Company is cognizant of employees’ public health rights and supports and promotes their good health, and encourages them to exercise. Health activities reduce various disease risks, such as obesity and diabetes, among others. At present, 800 employees participated in the project.
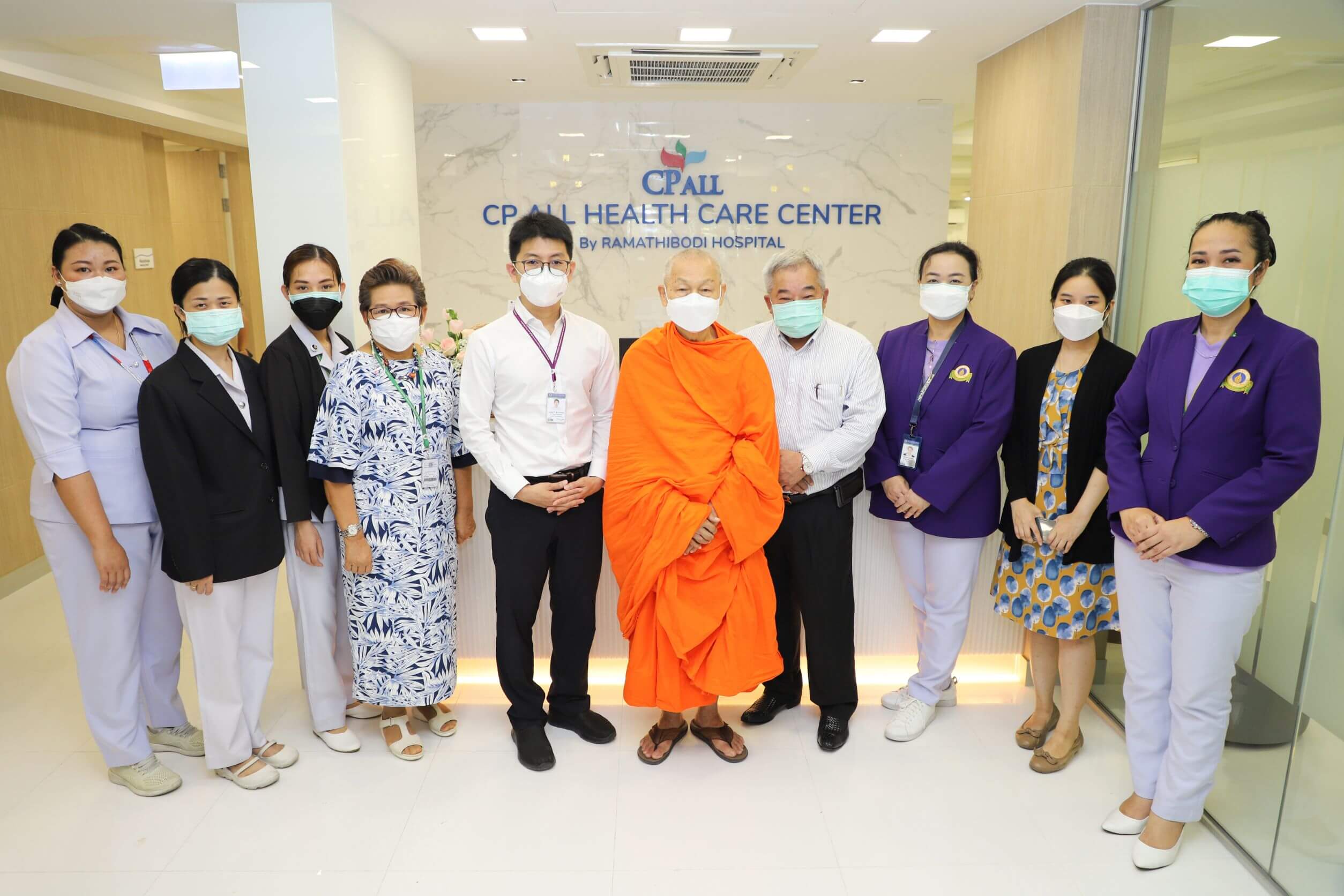
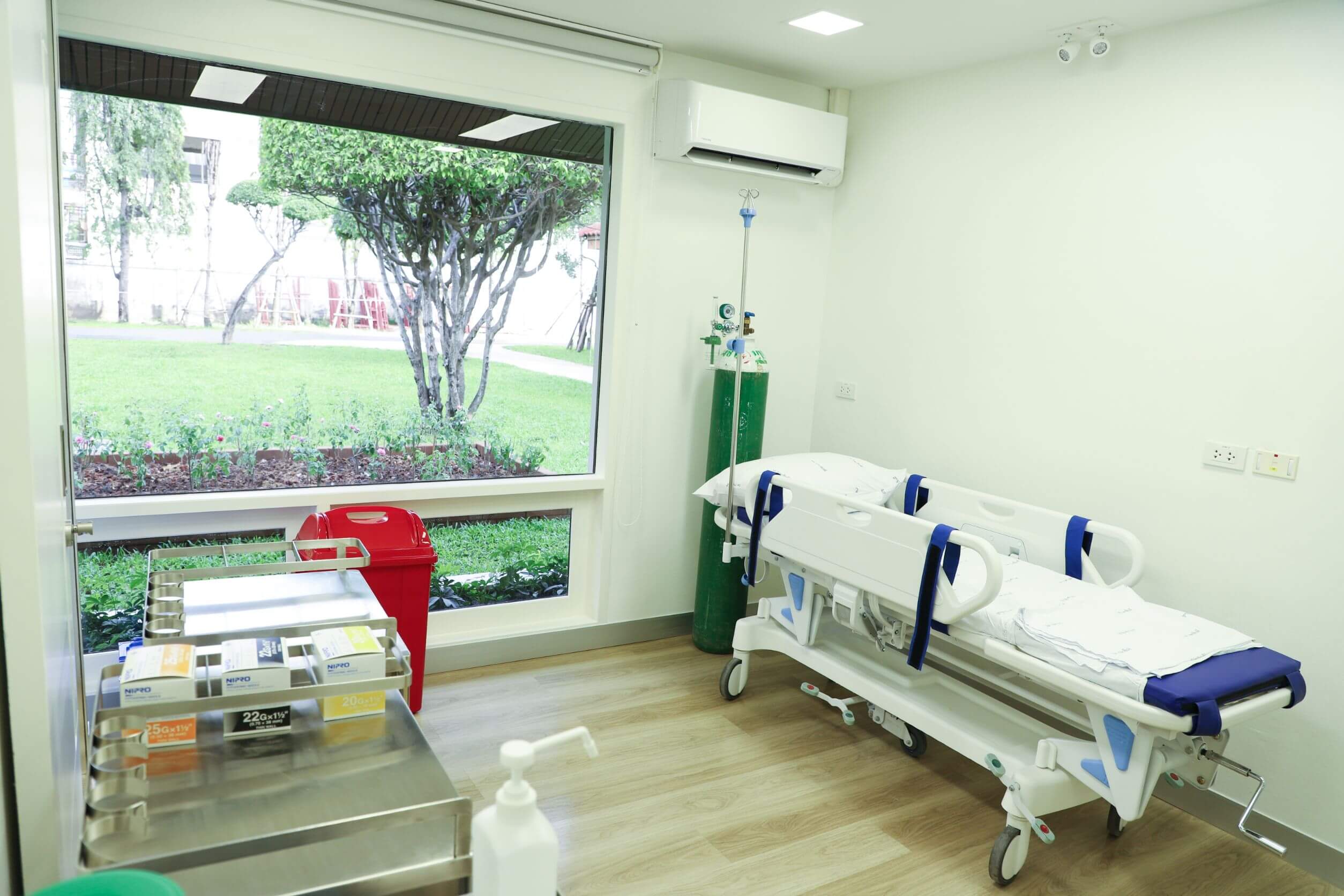
2. Safety Risks Reduction Program
Driving Safety Program for 7-Eleven Employees
The Company has ensured that its riders strictly comply with traffic rules, including the wearing of safety helmets; possession of a driver’s license, valid vehicle registration, and insurance; and have passed road safety training. In addition, the Company has also striven to promote the safety of 7-Eleven riders through the following measures.
![]() 1. Improve safety measures in using motorcycle vehicles |
|
![]() 2. Creation of a Safe Driving Culture |
|
![]() 3. Support for accident prevention equipment for riders |
|
![]() 4. Increased intensity of control measures and inspect rider practices |
|
![]() 5. Tested and piloted using Electric motorcycle |
Limits their speed to 50 kilometers per hour to reduce accident risks and help limit toxic emissions. Currently, there are 1,749 electric-powered bicycles in use at 7-Eleven stores |
The Company regularly monitors accident reports. In 2023, the company's 4-BS operations collaborated with the Honda Driving Training Center. With instructors specialized in safe driving, they conducted both theoretical and practical training sessions on standardized training grounds for employees. As a result, the 4-BS operational areas had no accidents resulting in fatalities or severe injuries (high-consequence). The Company aims to provide standardized training to all employees nationwide to reduce accident statistics to zero.
Freight Transport Safety Management Program
CP ALL aims to reduce the risk of workplace accidents for transportation contractors through a freight transport safety management program. This project aims to: 1) Establish safety standards for freight transportation. 2) Consistently communicate to raise awareness of safety among managers, staff, delivery unit personnel, freight transportation operators, and freight transport employees. The Company also promotes safe driving practices and prevention of potential accidents involving freight vehicles. 3) Reduce losses from freight transport accidents, both in terms of life and property, by reducing the number of freight transport accidents and minimizing delays in product delivery caused by such accidents. 4) Align with the sustainable development goals of the CP Group's "Zero Accident" strategy. This initiative targets all distribution centers nationwide by 2030, as follows:
TRAIN-THE-TRAINER
CP ALL has developed safety standards training for transportation employees using the TRAIN-THE-TRAINER approach. This aims to educate transportation contractors about safe driving practices and conduct inspections on freight vehicles and analyzes accidents that occur at distribution centers to identify preventive measures and solutions.
DRIVING CONTEST
The contest is a competition for safe and efficient driving among transportation employees, using GPS tracking and recording data of freight vehicles. The objectives are: 1) To encourage consistently safe and efficient driving behavior among transportation employees. 2) To utilize existing GPS technology for tracking freight vehicles effectively. 3) To reduce accidents and losses resulting from transportation accidents. Additionally, rewards are given to transportation employees with good driving behavior.
DRIVING BEHAVIOR MONITORING
Elevating the tracking of driving behaviors of transportation employees with GPS systems involves monitoring their driving behaviors using GPS technology. There is an automatic warning system in place to notify when speeding occurs beyond the standards. The receipt of warnings will affect procurement evaluations upon contract expiration and wage rate adjustments because risky behaviors increase the likelihood of accidents and result in losses for the Company.
The operation includes establishing rest stops for long-haul transportation contractors on routes exceeding 250 kilometers or taking more than 4 consecutive hours to travel. These stops must provide safe parking areas for contractors to rest and reduce fatigue from driving.
Safety Dojo Training for Production Line Contractors and Employees
CPRAM Co., Ltd. promotes awareness of safety behaviors among all contractors and employees to reduce work-related accident risks. This is done in all regional branches. The training involves an accident simulator, encompassing dressing station, the use of personal protective equipment, slip and fall danger simulation station, among others. This is essentially a training facility to serve as a comprehensive center for learning about safety. It involves setting up simulated stations to demonstrate the risks of accidents in various scenarios. This program aligns with the company's goal of achieving zero work-related accidents by 2030.
Impacts and Benefits
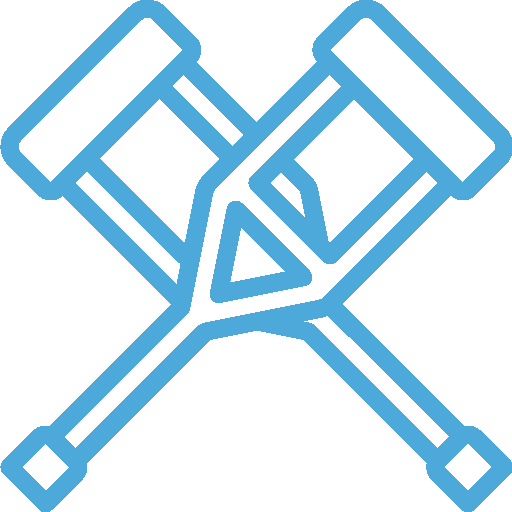
Reduction in Lost Time Injury Frequency Rate (LTIFR)
Security officer training program
CP ALL requires security companies under contract to provide training on the knowledge necessary to perform their duties, such as policies and procedures related to human rights. These include security as everyone's basic right, no violence against others, even if they are the perpetrators, security officers do not have the right to arrest anyone unless they are caught in the act of crime, and the accused has the right to be presumed innocent until proven guilty. All security officers must be fully aware of this guideline prior to working. In 2023, there were no human rights complaints against company security personnel. And 100% of outsourced contract security personnel are trained.
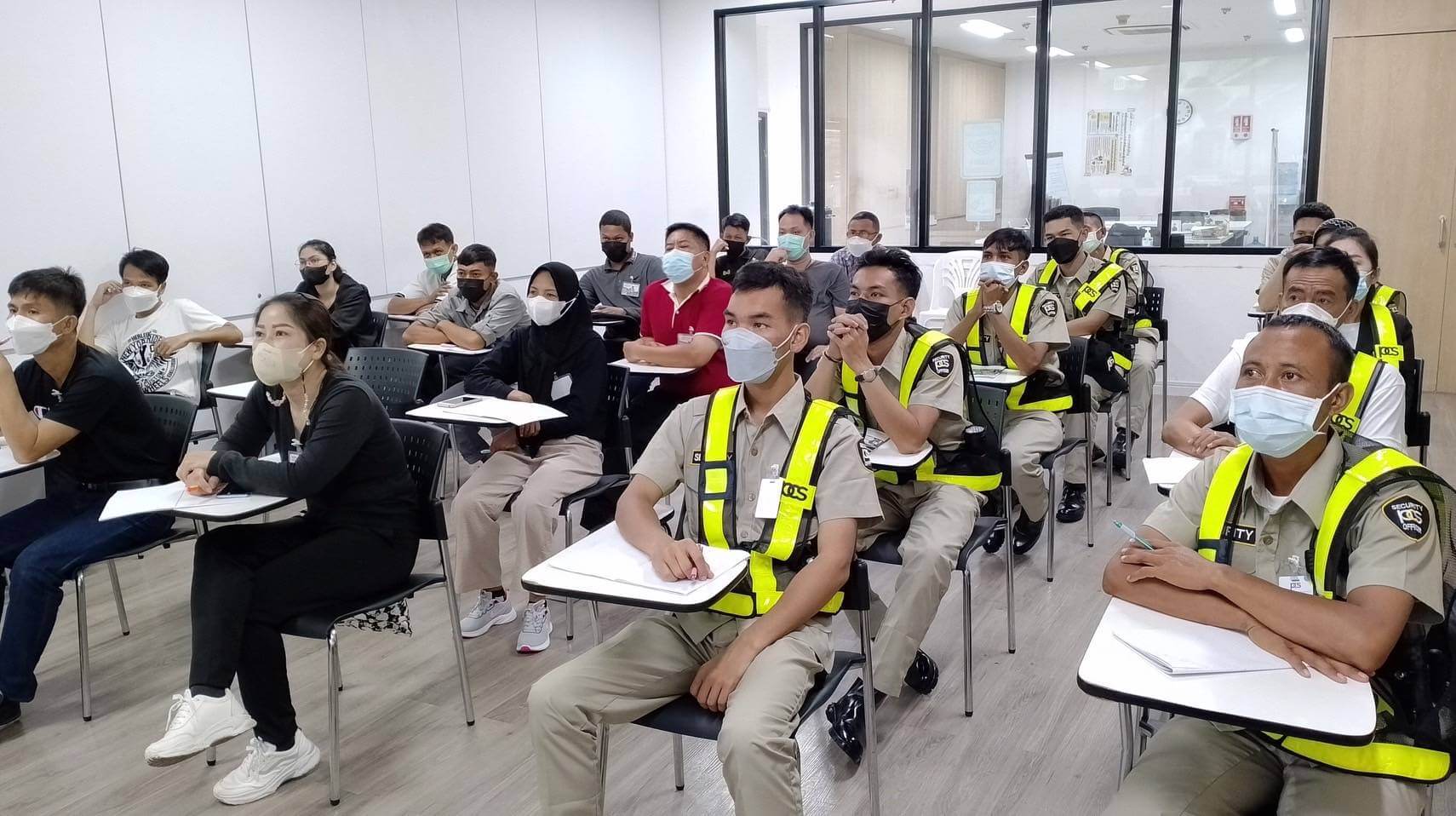
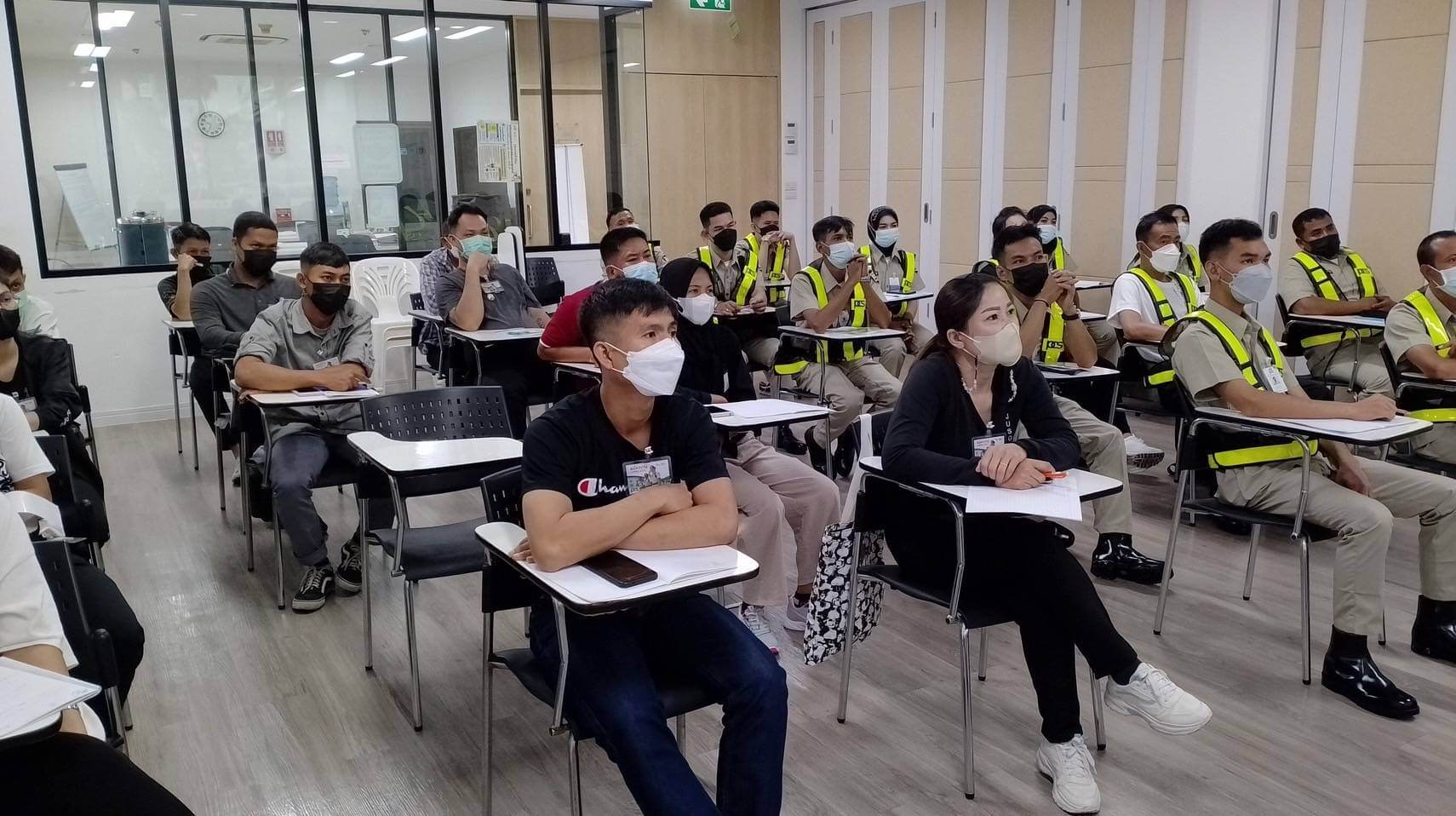
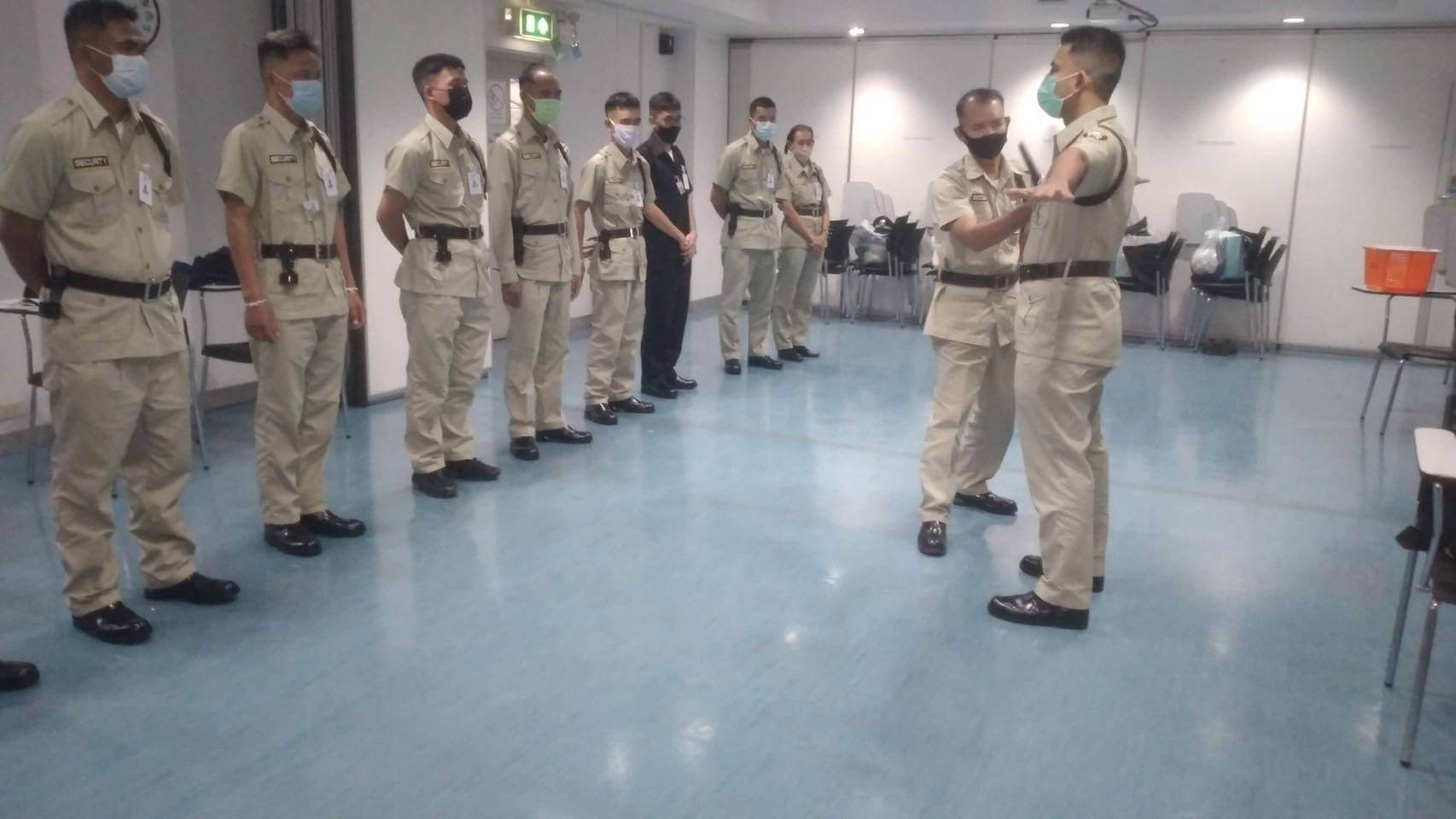
Impacts and Benefits
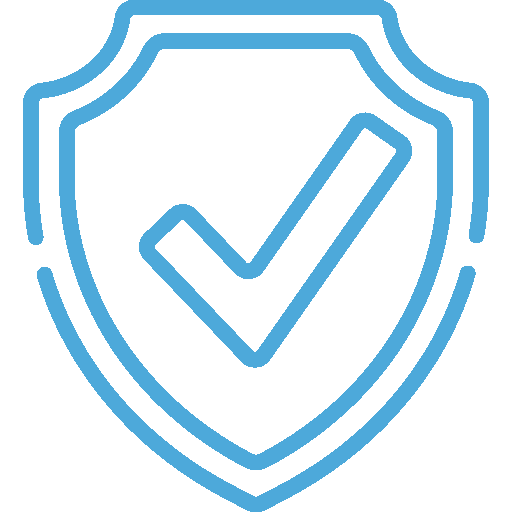
Outsourced contract security staff are trained
3. Ergonomic Risks Reduction and Stress Management Program
CP ALL Health Care Center
The Company operates a health care center project for the continuous care of employees' health, through the cooperation of medical personnel, including a team of doctors, nurses, and physiotherapists from Ramathibodi Hospital. There are 5 main areas of care, as follows: 1) General medical examinations 2) Specific diseases such as bone diseases, skin diseases, eye-ear-throat-nose diseases, etc. 3) Physical therapy (at the doctor's discretion), 4) Patient beds for recovery, and 5) Providing assistance in case of emergency illness or crisis. There are also other welfare benefits, such as prescriptions for employees with prescriptions or medical certificates without having to pay in advance, and employees can choose to receive medicines from home or the office. The Company promotes access to vaccines according to employees’ rights for employees at all levels and provides employees with additional vaccines for various diseases. The Company also provides rehabilitation services for patients with aches and pains, stiff muscles, weak legs, back pain, or suffered from office syndrome, along with providing consulting services and health care by expert physiotherapists. In 2023, there were 12,500
employees and executives participating in the project.
Office Syndrome Program
An online illness-preventing stretching program has been ongoing for 4 years and is supported by a specialist in physical therapy and Thai traditional medicine doctors from eXta Health & Wellness to provide health knowledge about Office Syndrome for executives and employees. And providing advice to employees on appropriate working ergonomics in order to prevent muscle pain. In 2023, there were 166 employees and management participated in the project.
Promoting Good Health for Employees Program “Massage for Health”
Promoting Good Health for Employees Program “Massage for Health” aims to be a program that employees can come to relax, reducing office syndrome problems, and improving overall employee health. The main target group consists of employees experiencing muscle fatigue and at risk of office syndrome, with a total of 132 participants.
Additionally, CPRAM Co., Ltd. (Khon Kaen), in collaboration with the safety department and the Traditional Thai Medicine Department of Sirindhorn Hospital, provides massage services for health, bone adjustment, and health issue consultations twice a month. This service has resulted in a 98% improvement in participants experiencing muscle fatigue.
Procedures to investigate work-related injuries, ill health, diseases and incidents
The investigation for work-related injuries
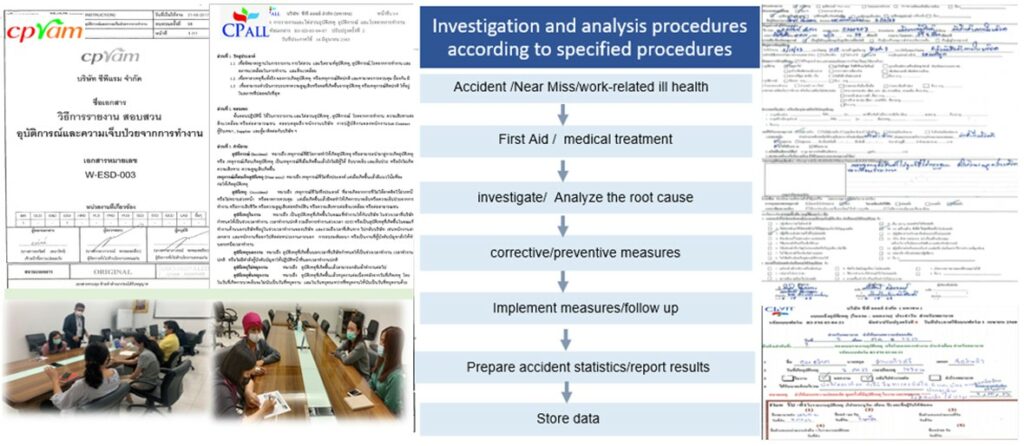
Work-related Injury Examination for the Rider Group
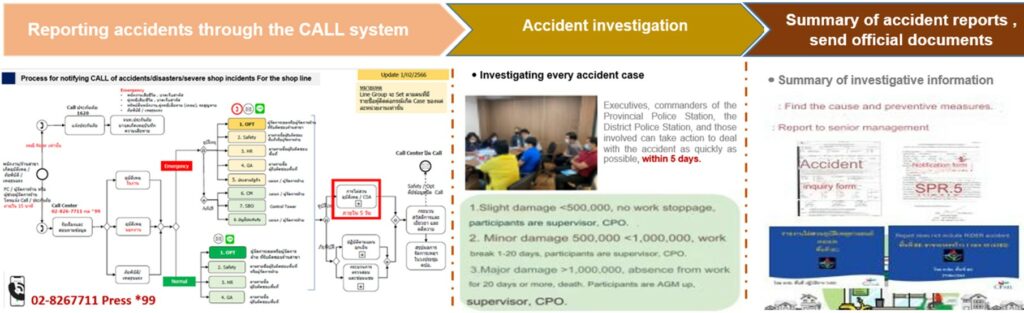
OHS training provided to employees and/or other relevant parties to raise awareness and reduce operational health & safety incidents
The Company gives great importance to knowledge development, employees’ performance, and raising awareness and communicating necessary information to stakeholders, including analyzing the need for training and conducting training, as well as offering knowledge sharing sessions and courses relevant to tasks at hands for employees to be able to perform tasks well and safe in risky operations. Examples of various relevant projects are as follows:
Safety Committee Workshop Project. The goal is the path to zero accidents

Safety and Environmental Management System Training Program for Personnel Development
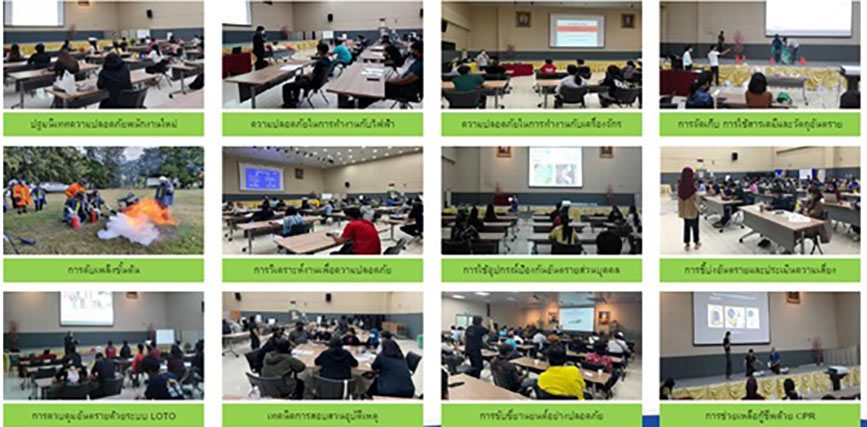
Training program to increase safe driving skills for 7-Eleven store staff
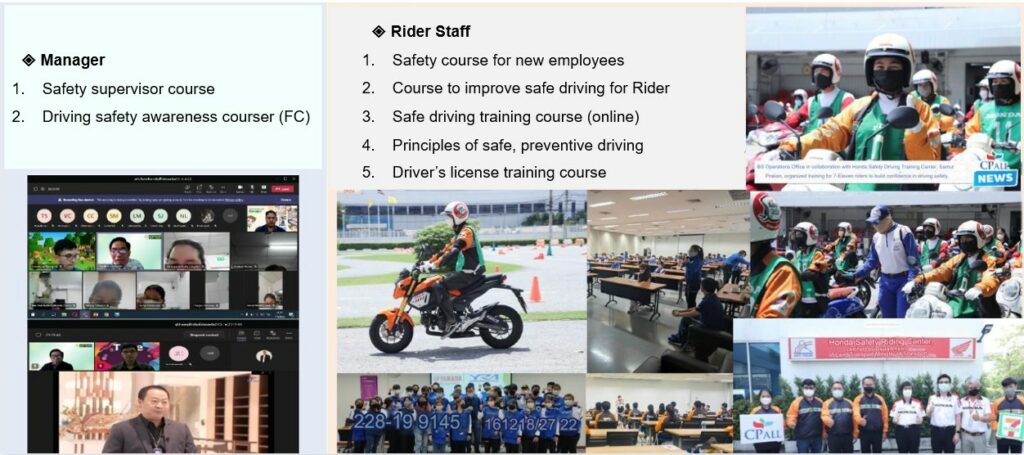
The program in raising awareness, changing safety behaviors for distribution center employees and transport contractors (Kiken Yochi Training : KYT)
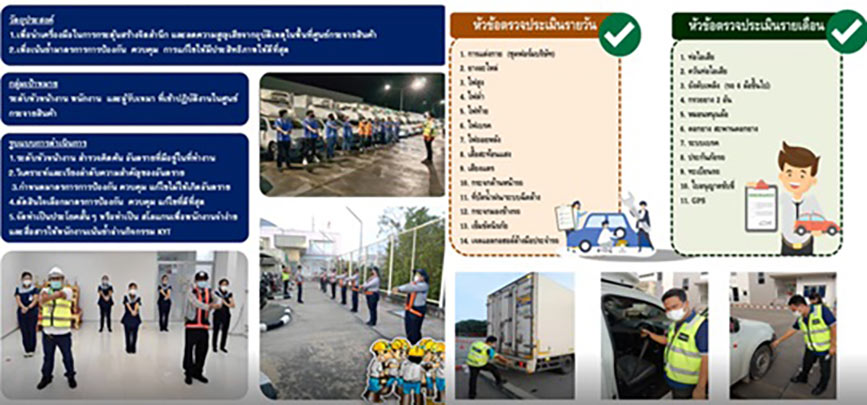
Training program for driving license test for PT vehicles and forklift vehicles, the coursework involves theory and practice for drivers
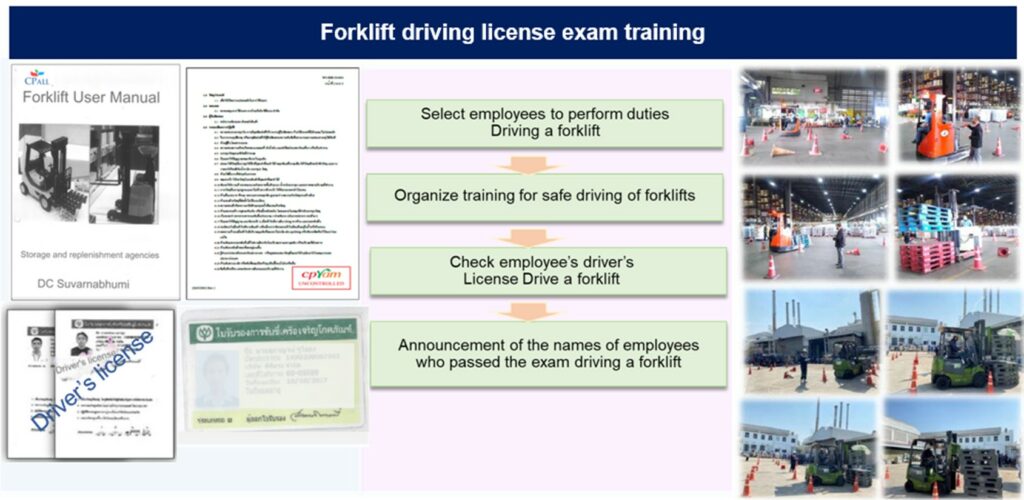
The program in construction contractor training on safety standards before working in 7-Eleven stores and distribution center areas and CP RAM factory area
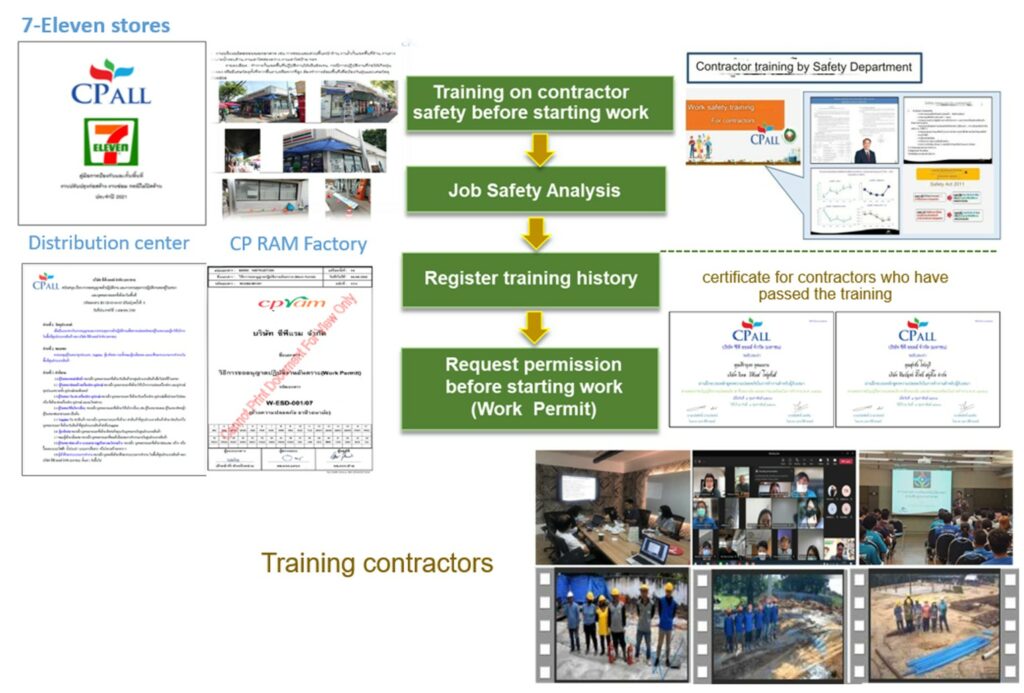
Transport Contractor Training Program: Professional Truck Driving Course
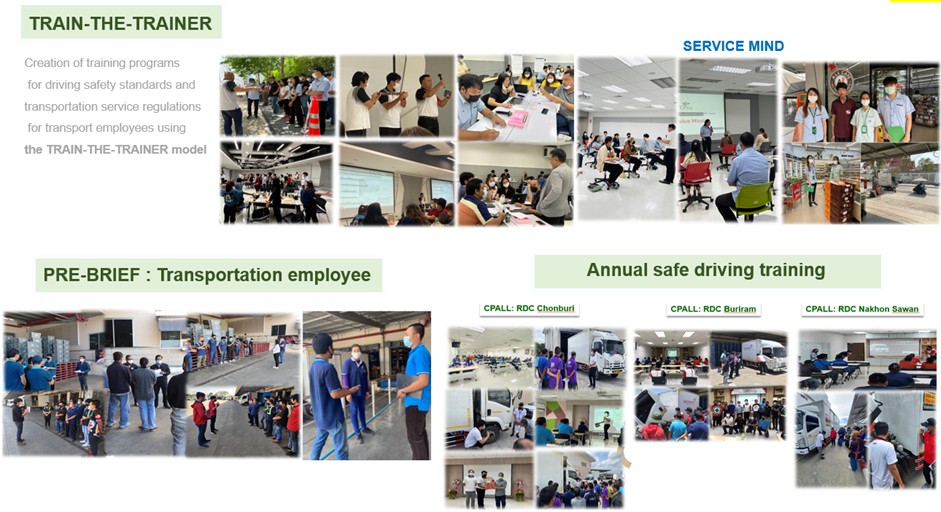
OHS criteria introduced in procurement and contractual requirements
The company focuses on procurement and hiring that may affect occupational health and safety. The Procurement Unit, that is involved with occupational health and safety, has established standards and guidelines for the procurement related to occupational health and safety for transport contractors, contractors, and external service providers. The tasks include preliminary qualifications of the safety-related contractor in a document that defines the scope and details of the mission the Company wants the contractor to perform, and other responsibilities related to the mission (Terms of Reference: TOR), as well as including the requirement of compliance with safety regulations and occupational health and work environment as one of the assessment/selection criteria for contractors, suppliers, and external service providers. This is to ensure that the procurement process is consistent with the law, risk aspects, the policies and measures to control risks related requirements, including occupational health and safety management system requirements.
Other Information
Performance Data of Occupational Safety, Health and Working Environment
GRI Standard | Required Data | Unit | 2019 | 2020 | 2021 | 2022 | ||||
Male | Female | Male | Female | Male | Female | Male | Female | |||
Employee | ||||||||||
403-9 (a) 2018 | - The number of fatalities as a result of work-related injury | Persons | 0 | 2 | 5 | 0 | ||||
0 | 0 | 2 | 0 | 2 | 3 | 0 | 0 | |||
- Fatalities rate | Cases/1,000,000work hours | 0 | 0.008 | 0.013 | 0 | |||||
0 | 0 | 0.02 | 0 | 0.013 | 0.013 | 0 | 0 | |||
- The number of high-consequence work-related injuries (excluding fatalities) | Persons | 0 | 1 | 3 | 2 | |||||
0 | 0 | 0 | 1 | 2 | 1 | 1 | 1 | |||
- High-consequence work-related injuries rate (excluding fatalities) | Cases/1,000,000work hours | 0 | 0.004 | 0.01 | 0.01 | |||||
0 | 0 | 0 | 0.01 | 0.01 | 0.004 | 0.01 | 0.004 | |||
- The number of recordable work-related injuries | Persons | 272 | 539 | 771 | 720 | |||||
170 | 102 | 252 | 287 | 351 | 420 | 366 | 354 | |||
- Recordable work-related injuries rate | Cases/1,000,000work hours | 1.22 | 2.14 | 2.00 | 1.93 | |||||
2.27 | 0.69 | 3.02 | 1.99 | 2.23 | 1.84 | 2.74 | 1.49 | |||
- Lost-Time Injuries Frequency Rate (LTIFR) | Cases/1,000,000work hours | 0.71 | 1.66 | 1.69 | 1.65 | |||||
1.28 | 0.43 | 2.21 | 1.38 | 1.80 | 1.62 | 2.22 | 1.29 | |||
- The number of hours worked | Hours | 222,630,585 | 251,718,321 | 386,155,115 | 372,331,111 | |||||
74,829,447 | 147,801,138 | 83,430,837 | 168,287,484 | 157,467,972 | 228,687,144 | 135,490,551 | 236,840,560 | |||
403-10 (a) 2018 | - The number of fatalities as a result of work-related ill health | Persons | 0 | 0 | 0 | 0 | ||||
0 | 0 | 0 | 0 | 0 | 0 | 0 | 0 | |||
- The number of cases of recordable work-related ill health | Cases | 0 | 0 | 1 | 0 | |||||
0 | 0 | 0 | 0 | 1 | 0 | 0 | 0 | |||
- Occupational Illness Frequency Rate (OIFR) | Cases/1,000,000work hours | 0 | 0 | 0.003 | 0 | |||||
0 | 0 | 0 | 0 | 0.01 | 0 | 0 | 0 | |||
Contractor | ||||||||||
403-9 (b) 2018 | - The number of fatalities as a result of work-related injury | Persons | 0 | 3 | 9 | 12 | ||||
0 | 0 | 2 | 1 | 8 | 1 | 7 | 5 | |||
- Fatalities rate | Cases/1,000,000work hours | 0 | 0.01 | 0.03 | 0.05 | |||||
0 | 0 | 0.02 | 0.01 | 0.05 | 0.01 | 0.07 | 0.03 | |||
- The number of high-consequence work-related injuries (excluding fatalities) | Persons | 0 | 0 | 2 | 1 | |||||
0 | 0 | 0 | 0 | 1 | 1 | 0 | 1 | |||
- High-consequence work-related injuries rate (excluding fatalities) | Cases/1,000,000work hours | 0 | 0 | 0.007 | 0.004 | |||||
0 | 0 | 0 | 0 | 0.01 | 0.01 | 0 | 0.01 | |||
- The number of recordable work-related injuries | Persons | 96 | 120 | 306 | 267 | |||||
68 | 28 | 71 | 49 | 186 | 120 | 153 | 114 | |||
- Recordable work-related injuries rate | Cases/1,000,000work hours | 1.51 | 0.52 | 1.00 | 1.01 | |||||
20.2 | 0.93 | .080 | 0.34 | 1.16 | 0.82 | 1.42 | 0.72 | |||
- Lost-Time Injuries Frequency Rate (LTIFR) | Cases/1,000,000work hours | 0.99 | 0.37 | 0.74 | 0.80 | |||||
1.28 | 0.67 | 0.52 | 0.28 | 0.73 | 0.75 | 1.10 | 0.59 | |||
- The number of hours worked | Hours | 63,698,344 | 232,938,058 | 306,063,307 | 264,671,376 | |||||
33,717,995 | 29,980,349 | 88,997,868 | 143,940,189 | 160,289,943 | 145,773,363 | 107,389,032 | 157,282,344 | |||
403-10 (b) 2018 | - The number of fatalities as a result of work-related ill health | Persons | 0 | 0 | 0 | 0 | ||||
0 | 0 | 0 | 0 | 0 | 0 | 0 | 0 | |||
- The number of cases of recordable work-related ill health | Cases | 0 | 0 | 1 | 0 | |||||
0 | 0 | 0 | 0 | 1 | 0 | 0 | 0 | |||
- Occupational Illness Frequency Rate (OIFR) | Cases/1,000,000work hours | 0 | 0 | 0 | 0 | |||||
0 | 0 | 0 | 0 | 0 | 0 | 0 | 0 |
Remark
1) Types of accident-related injuries cases of high-consequence work-related injuries of employees and contractor in 2022 include:
- Employees, 2 cases, disability type (loss of organs, limbs)
- Contractor, 1 case, type of disability (loss of organs, limbs)
2) In 2022, the scope of employee data reporting was expanded. Cover subsidiaries as follows:
- Ek-Chai Distribution Systern Co.,Ltd. Start reporting data from the year 2021 onwards
- CP ALL Plc. expanded its scope to cover Education area and CPRAM Co., Ltd. reports covering all areas
3) In 2022, the scope of contractor data reporting was expanded as follows:
- CP ALL Plc.report data of contractors hauling good within the distribution center
- Ek-Chai Distribution Systern Co.,Ltd. report data of construction contractor, facility Management contractor, security Officer, housekeeper, product introduction staff at the branch (PC), food shop staff for employees, shop staff for rent and transportation contractor
- CPRAM Co., Ltd. report data of contractor selling food in the factory, nurse and supplie
4) The formula for calculating safety data for the year 2022 is as follows:
- High-consequence work-related injuries rate (excluding fatalities) = Total number of work-related injury (cases) that results in an injury which the worker cannot expected to recover fully to pre-injury health status within 6 months over the reporting period X 1,000,000 hours worked / Number of hours worked (over the reporting period)
- Recordable work-related injuries rate = Total number of injuries (cases) at all levels including work-related injury from restricted work, beyond first-aid level, lost-day level to severity level over the reporting period X 1,000,000 hours worked / Number of hours worked (over the reporting period)
- Lost-Time Injuries Frequency Rate (LTIFR) = Total number of lost time injuries (cases) over the reporting period x 1,000,000 hours worked / Total hours worked (over the reporting period)
- Occupational illness Frequency Rate (OIFR) = Total number of occupational diseases (cases) over the reporting period x 1,000,000 hours worked / Total hours worked (over the reporting period)
Related policies and Guideline
Safety, Health and Working Environment Policy | Download |